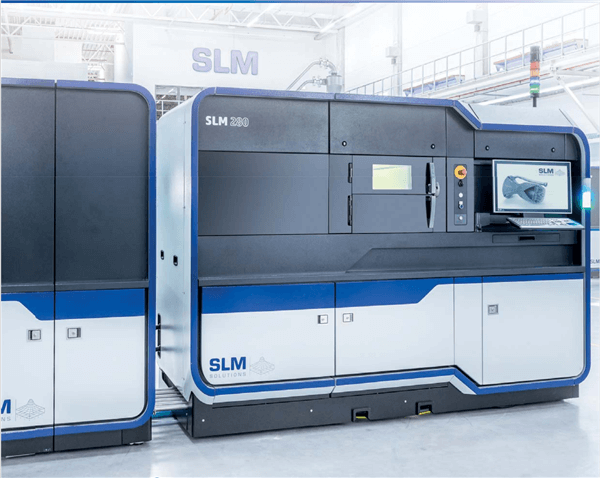
Online Professional 3D Printing Service
3D printing is usually achieved using digital technology material printers. It is often used to make models in the fields of mold manufacturing, industrial design, etc., and is gradually used for the direct manufacturing of some products. There are already parts printed using this technology.
3D printing technology has applications in jewelry, footwear, industrial design, architecture, engineering and construction (AEC), automotive, aerospace, dental and medical industries, education, geographic information systems, civil engineering, firearms, and more.
Advantages of 3D printing technology
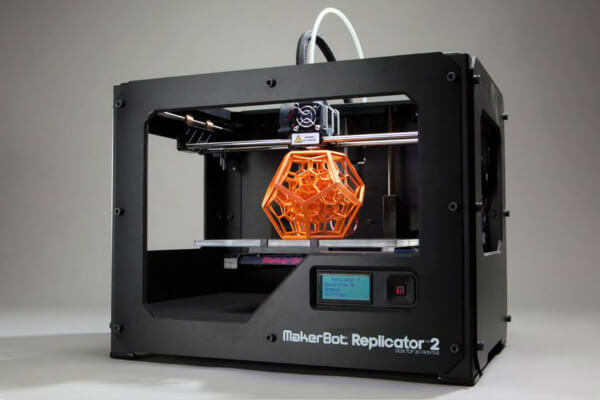
3D printing service type
The processing method of SLS is similar to SLA technology, but the liquid photopolymer is replaced with powder raw material, and the powder material is acted on with a certain scanning speed and energy. During the forming process, the laser parameters as well as the properties of the powder and the sintering atmosphere are important factors affecting the quality of the sintered forming. SLS rapid prototyping can produce the hardest prototypes, and can use a variety of raw materials, such as most engineering plastics, waxes, metals, ceramics, etc., the construction speed of parts is high, no post-correction of parts is required, and no design and construction support is required
SLS stands for Selective Laser Sintering, which is at the heart of this 3D printer. The key word here is sintering, which is the process of compacting and forming a solid material by heat and/or pressure without melting it to the point of liquefaction.
SLS (Selective Laser Sintering) printing fuse the powder (typically nylon powder) to form the part by laser technology. Without additional supporting materials, the SLS printed parts allow high flexibility and are very suitable for functional parts and moving parts from prototypes. Parts can be assembled or jointed.
SLA is a process using the principle of stereolithography, also known as selective curing of photosensitive resin, and is the earliest rapid prototyping technology. The process is: a resin tank is filled with liquid photosensitive resin, which is rapidly cured under the irradiation of an ultraviolet laser beam. At the beginning of the forming process, the liftable worktable is at the height of the layer thickness of the next section below the liquid surface. The resin is cured, thereby obtaining a resin sheet of this cross-sectional profile. Then, the worktable is lowered by the height of one layer of the sheet, and the cured resin sheet is covered by a new layer of liquid resin for the second layer of laser scanning curing, and the newly cured layer is firmly bonded to the previous layer, Repeat this until the entire product is formed. Finally, cleaning, removing support, secondary curing, and surface finishing are performed.
The photosensitive resin selective curing rapid prototyping technology is suitable for the production of small and medium-sized workpieces, and can directly obtain resin or similar engineering plastic products. The prototype of SLA rapid prototyping has good surface quality, high system resolution and high forming accuracy.
SLA (Stereo lithography Appearance) printing is applicable to presentation prototypes, concept models, and translucent prototypes. To create parts, the process cures the photopolymer layer by layer by UV light. SLA technology becomes popular because of the result of high resolution.
3D printing process introduction – SLA light curing molding
The full name of SLA in English is Stereo Lithography, and in Chinese it is light curing technology. The principle is to use ultraviolet light to irradiate the liquid photosensitive resin to polymerize, to solidify layer by layer and generate a three-dimensional solid molding method. The accuracy of workpieces prepared by SLA can reach ±0.1/100mm (10 filaments), which is the earliest commercialized 3D printing technology.
SLA is widely used in design verification in industrial, automotive, medical, consumer electronics and other industries.
The SLA material is a liquid photosensitive resin, and the workpiece surface is smooth and can be subjected to post-processing such as electroplating, painting, and coloring.
Compared with the nylon material formed by SLS sintering, the photosensitive resin material is relatively brittle and low in toughness. Moreover, design support is usually required during the printing process to ensure the quality of the printed product.
Advantages of SLA technology:
- The light curing molding method is the earliest rapid prototyping manufacturing process, which has a high degree of maturity and has passed the test of time.
- The processing speed is fast, the product production cycle is short, and no cutting tools and molds are required.
- Prototypes and molds with complex structures or shapes that are difficult to form using traditional methods can be processed.
- Personalized products can be customized.
- Compared with traditional prototype processing, the cost is lower and the pricing method is transparent.
Disadvantages of SLA technology:
- The material is photosensitive resin with limited strength, stiffness and heat resistance. Over time, the resin will absorb moisture in the air and turn yellow when exposed to ultraviolet rays, resulting in warping and deformation of the soft and thin parts, which is not conducive to long-term storage. Only suitable for verification of product appearance.
- The material is single. Generally, the more mature materials are photosensitive resin (SLA), nylon (SLS), and nylon fiber (SLS). There are not as many material choices as CNC machining.
Compatible with a broad range of materials and used for prototyping or end-use production, FDM extrudes melted filament through a nozzle, building the part layer by layer.
Maximum build size
Up to 500 x 500 x 500 mm (19.68” x 19.68” x 19.68”)
Lead time
From 3 business days
Dimensional accuracy
± 0.5% with a lower limit of ± 0.15 mm (± 0.006″)
Layer height
100-300 μm
Infill 20-100%
- All unfused powder is removed via bead blasting (first) and air blasting (second)
- Air pressure range of 2 – 5 bar or 29 – 72.5 psi
- Glass beads with diameter 70-110 microns
- No additional post-processing
3D Print Prototyping Projects Case
3D Printing Service FAQ
What Members Are Saying About Us
Lorem ipsum dolor sit amet, consectetur adipiscing elit. Ut elit tellus, luctus nec ullamcorper mattis.
“
“
Many Major
Companies Trust Us
Lorem ipsum dolor sit amet, consectetur adipiscing elit. Ut elit tellus, luctus nec ullamcorper mattis, pulvinar dapibus leo.