industrial manufacturing
Soaring above expectations
Our industrial machine shop services include aerospace parts machining and machined aerospace products. At Cox Manufacturing, we have a two-pronged approach to the stratospheric material and process requirements of the aerospace industry. We rise to the challenge of crafting high precision components designed for modern flight vehicles, while consistently maintaining the rigorous standard of on-time delivery and reliable quality we’ve upheld for half a century.
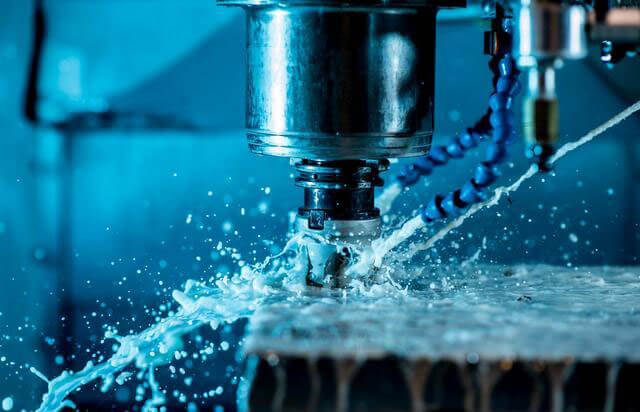
industrial manufacturing Machining Services
Professionals in the Aerospace Industry know they can count on our full complement of machining capabilities:
- The exceptional precision of CNC Swiss machining
- Multi spindle cam automatics
- CNC turning and milling up to 12-axis machine centers
- An Esprit CAD/CAM system to precisely produce the most elaborate geometries (complete equipment list)
Certifications & Standards
Our mastery of high performance materials such as titanium, stainless, exotic alloys and high temperature plastics makes us the rising star in aerospace component manufacturing. Our ISO 9001:2015 quality system, compliance with ITAR controls, and extensive knowledge of DFARS materials source requirements makes Cox fully compatible with aerospace industry expectations.
In an industry where a mission’s success hinges on the quality of each individual component, Cox takes pride in its track record as a trusted supplier to the innovators in aerospace design.
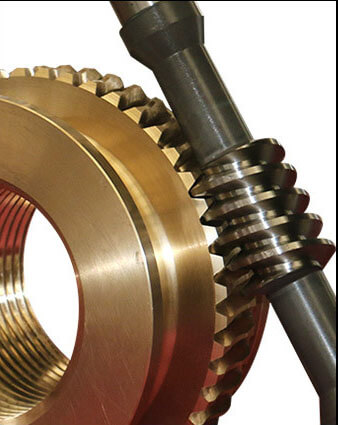
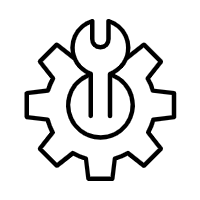
Safe And Machining Capacity
With strong production capacity, more than 100 CNC machining capabilities, up to 500 professional CNC engineers, convenient transportation can quickly deliver your goods.
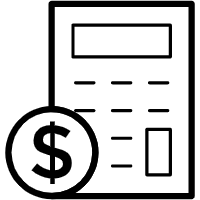
Professional Quick Quote
Professional quotation engineers can give price and delivery date within one working day, with 20% discount for the first order. Accept drawings of various types of documents, including STEP, Mesh, Parasolid, and ACIS files.
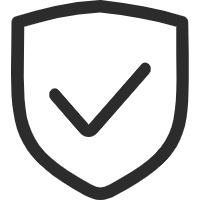
Quality Assurance
The company has passed EN9100&ISO9001 Certification,Delivery in as fast as 5 days /100% Inspection /FullProeess Measurement Report /3D Scanning Digital AnalogComparison /Pree Return and Exchange of Defective Products.
Rapid Manufacturing on Demand
In industrial manufacturing, products that have just been developed or designed usually need to be prototypes, also known as prototypes. Prototypes are the first step to verify the feasibility of products. Make targeted improvements to the defects until the deficiencies cannot be found from individual prototypes. At this point, it is usually necessary to carry out a small amount of trial production to find out the insufficient improvement in the batch. The designed products are generally not perfect or even unusable. Once the direct production is defective, it will be completely scrapped, which greatly wastes manpower, material resources and time; while the prototype is generally a small number of samples, the production cycle is short, and the loss of manpower and material resources is very small. Quickly find out the deficiencies of product design and improve it, and provide sufficient basis for product finalization and mass production.
The characteristics of CNC machining of hand model
- The degree of automation is high, and the production efficiency is very high. Except for blank clamping, all other processing operations can be completed by CNC machine tools. If combined with the automatic loading and unloading method, it is a basic part of the unmanned control factory. CNC machining reduces the labor of the operator, improves the labor conditions, and saves the processes and auxiliary operations such as marking, multiple clamping and positioning, and testing, and effectively improves the production efficiency.
- Adaptability to CNC machining objects. When changing the processing object, in addition to changing the tool and solving the blank clamping method, only reprogramming is required, and other complex adjustments are not required, which shortens the production preparation cycle.
- High machining accuracy, stable quality, machining dimensional accuracy between d0.005-0.01mm, not affected by the complexity of the parts, because most of the operations are automatically completed by the machine. Therefore, the size of batch parts is increased, and the precision control The position detection device is also used on the machine tool, which further improves the precision of precision CNC machining.
- CNC machining has two main features: one is that it can greatly improve the machining accuracy, including machining quality accuracy and machining time error accuracy; the other is the repeatability of machining quality, which can stabilize machining quality and maintain the quality of machined parts.
.
industrial Machining Materials
From prototyping to full production runs. Our wide range of CNC lathes and turning centers will allow you to produce highly accurate, high quality parts to meet even your most stringent requirements.
AEROSPACE MACHINING MATERIALS | ||
Alloys | Stainless Steel | |
METALS | Aluminum | Precision Steel |
Brass | Titanium | |
Copper | Special Alloys | |
PVC | UHMW | |
PLASTICS | Nylon | Ultem |
Delrin | PEEK | |
PTFE | Acetal |
Top industrial Applications
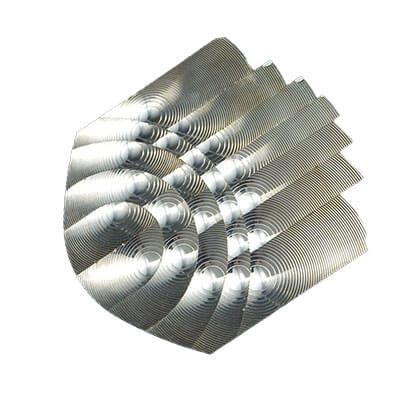
Quality
Quality is an important aspect that must be achieved in any aerospace part. Our ISO 9001:2015 certification means that our production lines feature advanced technologies that give exact manufacturing precision and accuracy. We conduct routine inspections on all aerospace parts prototypes we manufacture. These inspections are conducted during actual manufacturing sessions as well as on aerospace parts at the end of a production line. We also conduct numerous quality checks and testing that all the parts we produce must satisfy. The tests are approved by regulating aviation authorities and focus on ensuring that parts have the right structural strength, numerical specifications, and performance. Through this rigorous testing and inspection process, any defective component is identified and placed in isolation.
Tolerances
Limits for nominal size | Plastics (ISO 2768- m) | Metals (ISO 2768- f) |
---|---|---|
0.5mm* to 3mm | ±0.1mm | ±0.05mm |
Over 3mm to 6mm | ±0.1mm | ±0.05mm |
Over 6mm to 30mm | ±0.2mm | ±0.1mm |
Over 30mm to 120mm | ±0.3mm | ±0.15mm |
Over 120mm to 400mm | ±0.5mm | ±0.2mm |
Over 2000mm to 4000mm | ±2mm |